

This procedure is designed to avoid warpage. When welding sheet metal, a short, one-inch bead is laid down, then a pause in time, while the welder moves to another point to weld. Many inexpensive MIG welders that run on 110-volts will have a high current, but only for a short time. Mig welding is the best choice for welding automotive body panels. With shielding gas, you to get clean, good looking welds on thin sheet metal. The shielding gas is fed through the gun, and basically "suffocates" the weld area from oxygen. However, flux-core is not the best choice for thin sheet metal.Īs it's name implies, the metal inert gas (MIG) welding process uses a shielding gas to "shield" the molten puddle from the atmosphere. This process is effective when welding outdoors, in windy conditions, or on dirty materials. The two major limitations of Mig welding is that it can be difficult to use outdoors (wind can blow away your shielding gas), and that you have to cart around a gas bottle.įlux-core welding, also known as wire-feed welding, does not require gas, instead using a flux-cored wire to shield the arc. These small, gasless welders sell for as little as $150, but they are very limited as to what they can actually weld.īoth the Mig and flux-core techniques are relatively easy to learn and give clean welds on steel, aluminum and stainless.īoth have the capability to weld materials as thin as 26-gauge. Most inexpensive wire-feed welders run on standard 110v current and are very portable. In other words, you can weld with shielding gas or without shielding gas.
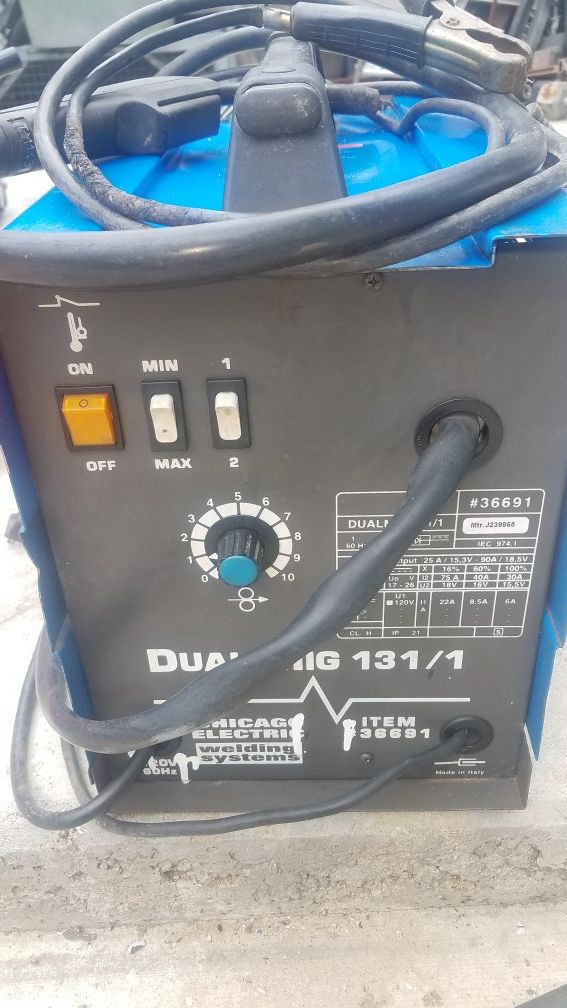
Two types of welding can be done with a Mig welder - Mig and flux-core. MIG welding is faster and more economical than other processes, and well suited for thin metal.Īlthough set-up time can be time-consuming, the actual MIG welding process is relatively quick. With a good quality machine, the home hobbyist and classic car enthusiast can repair automotive sheet metal as well as fabricate brackets, repair exhaust systems, make special tools, etc. Of the four welding processes, the most versatile for all-around automotive use is the MIG welder. It is also the most expensive welder to buy. TIG welding is neat and precise, but the most difficult to learn. It's great for all kinds of garage projects, but not a good choice for thin sheet metal. Stick, or Arc welding, is easy to learn, doesn't require a gas bottle, but does require a lot of clean-up. However, gas welding is hard to learn and difficult to weld thin metal. Having a rosebud tip allows you to cut through thick metal. Having an Oxy-Acetylene set-up in your home garage allows you to heat up stubborn bolts and pre-heat parts. Gas welding is the oldest form of welding. The most common types of welders are Gas, Stick, TIG, and MIG. Some are easier to get started with than others, some are less expensive than others, and some take more time to master. To help select the best welder for automotive repair and restoration, you should be familiar with the different types of welding processes. Which leads me here, searching for a suitable replacement. Seems that Solar was bought out by Century Manufacturing sometime in the nineties, then Century was acquired by Lincoln Electric in 2003.
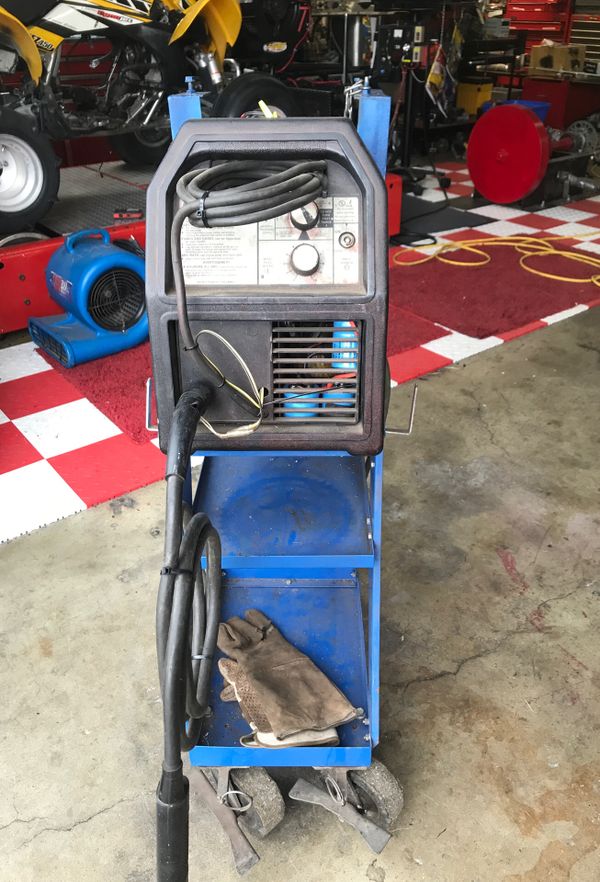
One said, "We don't work on them", the other said "We can't get parts for them." Parts and service are nowhere to be found. The Solar 2150 MIG machine had been doing a good job with sheet metal and steel up to 3/16", but always struggled with anything thicker.Īs of late, it's been giving me problems, and recently stopped working (fan comes on, no spark).
